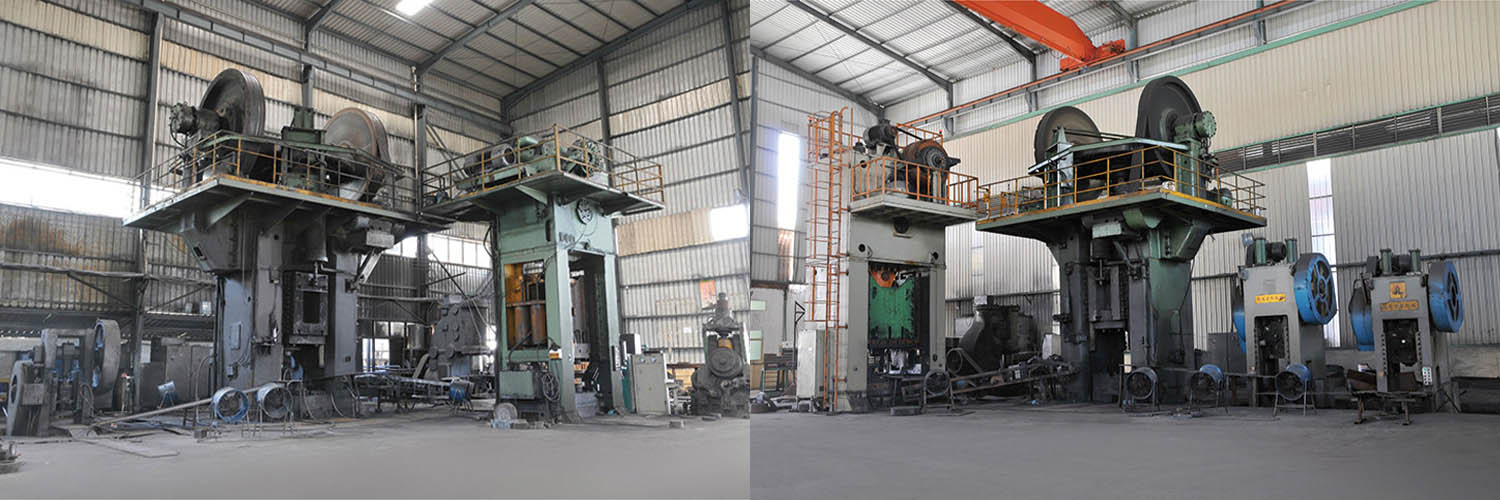
OUR CAPABILITIES
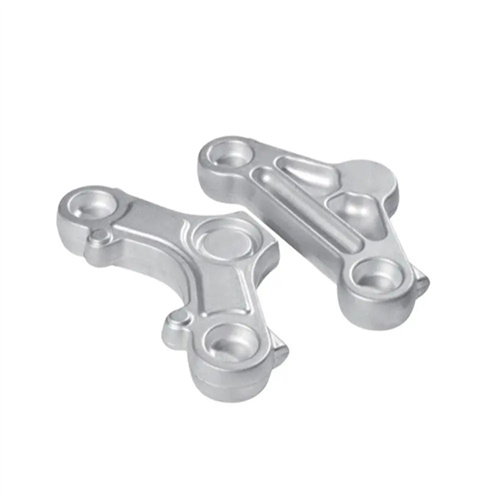
Custom Forging Parts
Custom forging parts are specialized components manufactured to meet specific design and performance requirements. This process involves shaping metal using localized compressive forces, often with a hammer or die, to create parts with superior strength and durability. Custom forging is ideal for industries that require unique, high-performance parts such as aerospace, automotive, and heavy machinery.
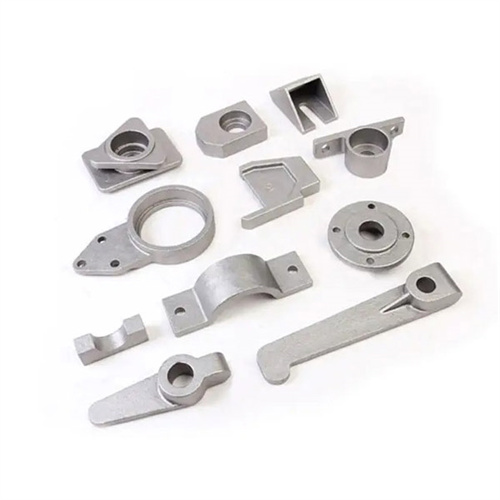
Hot Press Forging
Hot press forging is a manufacturing process where metal is heated to a high temperature and then shaped using a press to apply continuous pressure. This method is particularly effective for producing complex shapes with high precision and excellent mechanical properties. It is commonly used for creating large, high-strength components in industries like automotive, construction, and energy.
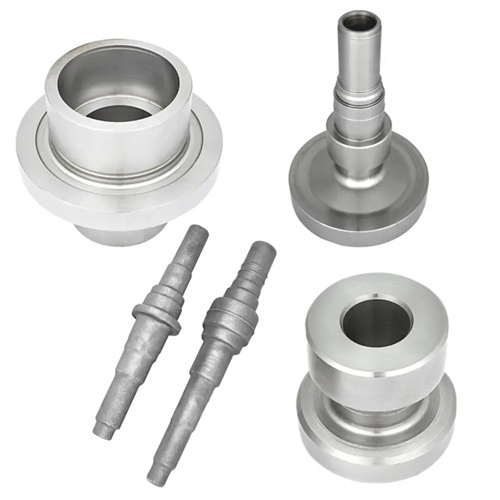
Steel Forging
Steel forging involves shaping steel using compressive forces, typically while the metal is heated to enhance its malleability. This process results in parts with exceptional strength, toughness, and resistance to wear and fatigue. Steel forging is widely used in applications requiring high durability, such as gears, shafts, and structural components in the automotive, construction, and machinery sectors.
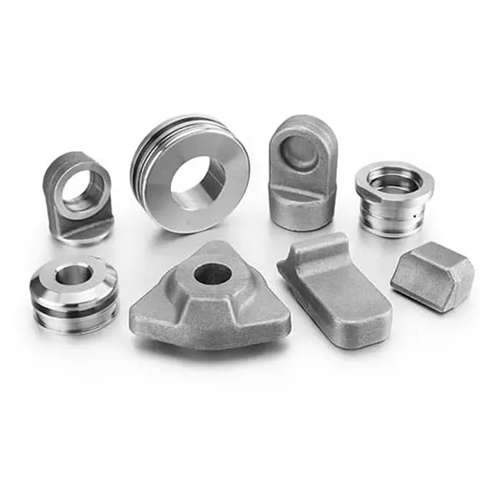
Aluminum Forging
Aluminum forging is the process of shaping aluminum alloys using compressive forces, often at elevated temperatures. This method produces lightweight yet strong components with excellent corrosion resistance and thermal conductivity. Aluminum forging is commonly used in the aerospace, automotive, and electronics industries, where weight reduction and performance are critical.
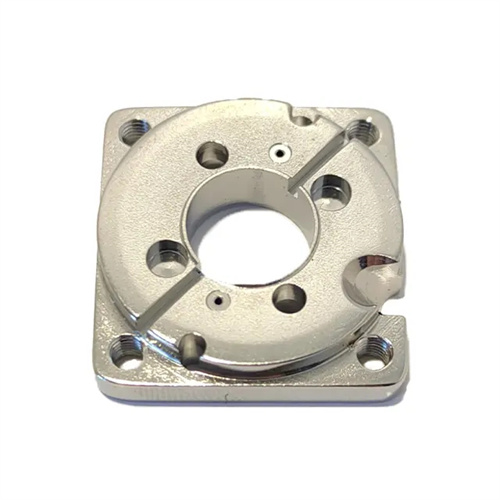
Alloy Steel Forging
Alloy steel forging involves shaping steel that has been combined with other elements like chromium, nickel, or molybdenum to enhance its properties. This process results in components with superior strength, hardness, and resistance to wear and corrosion. Alloy steel forgings are essential in demanding applications such as oil and gas, power generation, and heavy machinery, where high performance under extreme conditions is required.
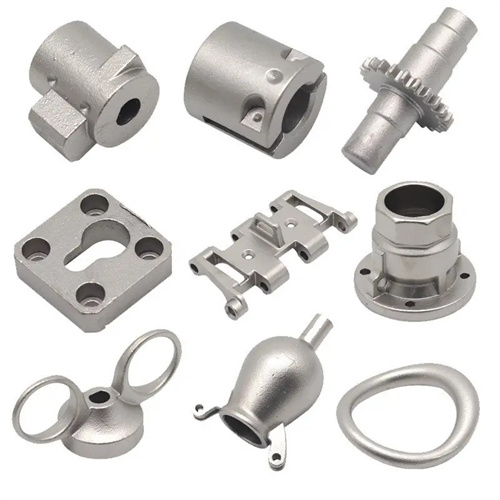
Stainless Steel Forging
Stainless steel forging is the process of shaping stainless steel, a corrosion-resistant alloy containing chromium, using compressive forces. This method produces parts with excellent strength, durability, and resistance to rust and staining. Stainless steel forgings are widely used in industries like food processing, medical devices, and marine applications, where hygiene, longevity, and resistance to harsh environments are crucial.
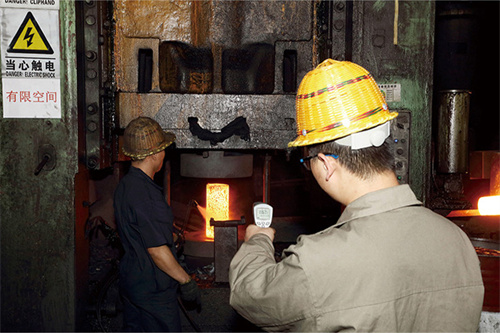
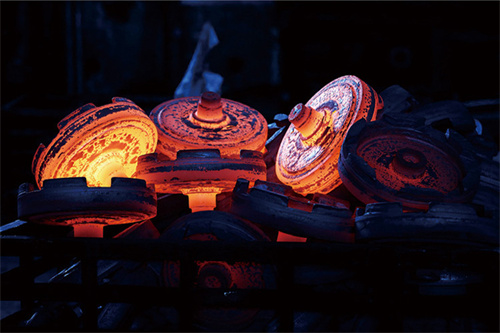
Forging Parts Manufacturer of China
As a leading forging parts manufacturer in China, we focus on providing high-quality customized forging solutions to global customers. In the field of hot forging, we have advanced hot forging equipment and mature process technology, which can accurately control key parameters such as temperature and pressure during the forging process, ensuring that every hot forging part has excellent mechanical properties and dimensional accuracy.
Our products cover a variety of material types. In terms of steel forging, whether it is ordinary steel or alloy steel, we can use exquisite forging techniques to create high-quality parts that meet various strict standards. For stainless steel forging, we fully utilize the corrosion resistance and high strength characteristics of stainless steel to produce parts widely used in fields such as food, medical, chemical, etc. that require high hygiene and corrosion resistance performance. In the field of aluminum forging, due to the lightweight and high-strength characteristics of aluminum materials, the aluminum forged parts we manufacture are highly favored in industries such as heavy machinery, general machinery, rail transit, energy, and construction.
Multiple Large-scale Press Forging Production Lines
As a leader in China’s forging industry, we are committed to providing comprehensive and high-quality customized forging solutions to global customers. Our company has established a good reputation in the industry with advanced production equipment, perfect process flow, and excellent quality control system.
Our company has invested heavily in equipment introduction and upgrading, and currently has multiple large-scale press forging production lines such as 1000T, 1600T, 2500T, 4000T, 8000T, etc. These advanced equipment can meet the production needs of forging parts of different specifications and materials. Whether it is small precision parts or large complex forgings, they can be accurately forged to ensure the dimensional accuracy and mechanical performance of products. At the same time, we are equipped with a ring rolling production line and a swing rolling production line, further enriching the forging process and producing various ring forgings and special shaped forgings, expanding the application fields of our products.
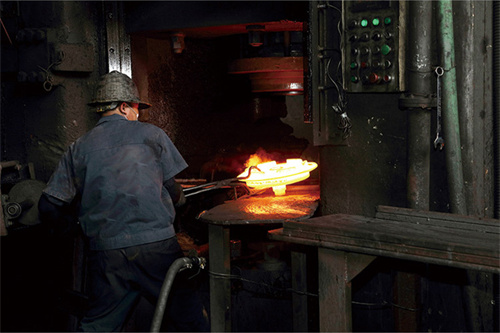
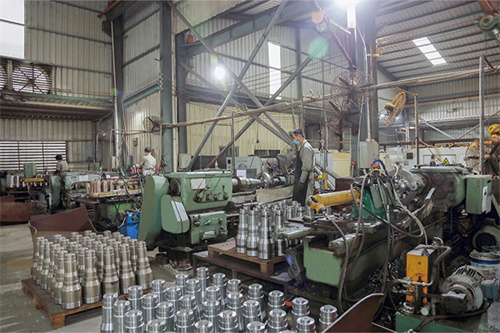
Complete Production Supporting Facilities
To achieve one-stop production services from raw materials to finished products, Our company has established a complete production supporting system. We have various machining workshops equipped with over 100 advanced deep processing machines, which can perform high-precision turning, milling, drilling and other machining operations on forged parts, ensuring that the parts meet the final design dimensions and surface quality requirements.
Relying on advanced equipment and a comprehensive production system, our company has strong production capabilities. At present, it has the ability to produce 30000 tons of forged parts and 300000 sets of excavator chassis components annually. The heat treatment workshop uses advanced heat treatment processes to perform quenching, tempering, annealing, and other treatments on forgings, effectively improving the material’s microstructure and properties, and enhancing the overall quality of products. In addition, our company has established a professional physical and chemical testing center equipped with advanced testing equipment, which can conduct comprehensive physical and chemical performance testing on raw materials, semi-finished products, and finished products, and strictly control product quality.
OUR SERVICES
Material Selection and Optimization
We can provide material selection recommendations and optimization services based on customer product needs: recommending suitable forging materials (such as carbon steel, alloy steel, stainless steel, etc.). Optimize the material formula based on the product's usage environment, such as high temperature resistance, corrosion resistance, wear resistance, etc. Provide material performance testing services to ensure that materials meet design requirements.
Technical Consultation
We have rich experience and technical accumulation, and can provide customers with the following support: process optimization: improving forging processes, enhancing production efficiency and product quality. Defect analysis and resolution: Assist customers in analyzing forging defects (such as cracks, folds, oxidation, etc.) and provide solutions. Cost control suggestion: Reduce production costs by optimizing design and processes.
Mold Design and Manufacturing
We will design high-precision and durable molds based on the part drawings provided by the customer. The types of molds include die forging, cold forging, and precision forging molds, and high hardness tool steel is often used as the material. In addition, for special needs, we support customized design and trial production of molds to ensure that we meet the diverse production requirements of our customers.
Products Showcase
OUR CERTIFICATES
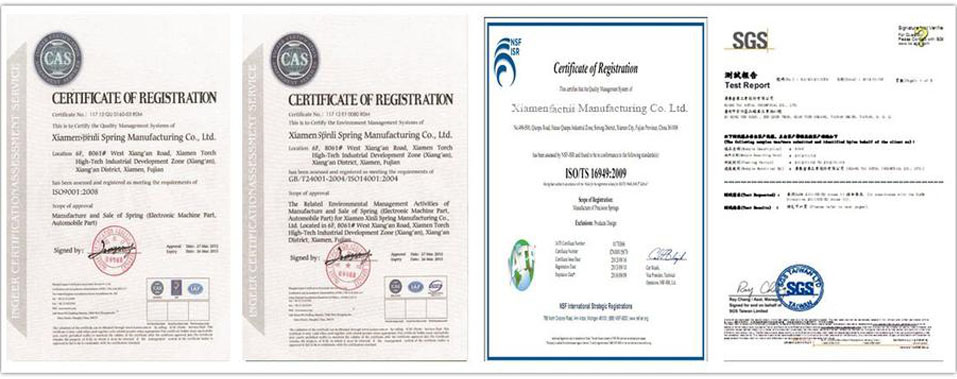