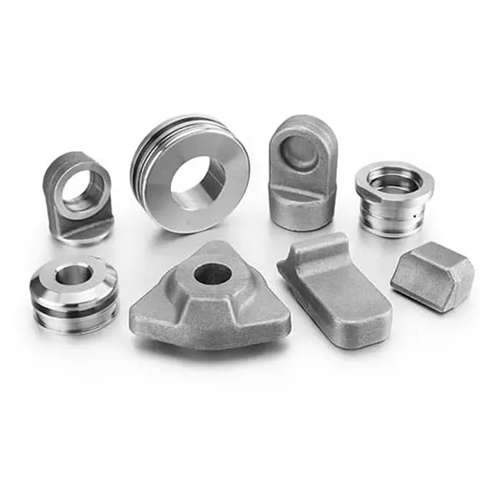
Aluminum Forging
Aluminum forging is a manufacturing process that involves shaping aluminum into desired components using compressive forces, typically at high temperatures. Aluminum is a lightweight, non-ferrous metal known for its excellent strength-to-weight ratio, corrosion resistance, and thermal and electrical conductivity. Forging enhances the mechanical properties of aluminum by refining its grain structure, resulting in components with superior strength, durability, and fatigue resistance.
Aluminum forging can be performed using various techniques, including hot forging, cold forging, and hot press forging, depending on the application requirements. The process is widely used in industries that require lightweight, high-performance components capable of withstanding demanding conditions.
Advantages of Aluminum Forging
Lightweight: Aluminum is significantly lighter than steel, making it ideal for applications where weight reduction is critical.
High Strength-to-Weight Ratio: Forged aluminum components offer exceptional strength and durability without adding extra weight.
Corrosion Resistance: Aluminum naturally forms a protective oxide layer, making it highly resistant to corrosion.
Excellent Thermal and Electrical Conductivity: Aluminum forged parts are widely used in applications requiring heat dissipation or electrical conductivity.
Customizability: Aluminum forging allows for the production of custom parts with complex geometries and precise dimensions.
Cost-Effectiveness: Forging reduces material waste and minimizes the need for secondary machining, lowering production costs.
Applications of Aluminum Forging
Rail Transit
In the rail transit industry, aluminum forging is used to produce lightweight and durable components for trains and rail infrastructure. Weight reduction is essential for improving energy efficiency and reducing wear on tracks.
Bogie Frames: Forged aluminum bogie frames reduce the weight of rail vehicles, improving energy efficiency and reducing track wear.
Brake Systems: Aluminum forged brake components, such as calipers and discs, provide the strength and durability needed for reliable braking performance.
Seat Frames: Forged aluminum seat frames are lightweight and durable, enhancing passenger comfort and reducing the overall weight of rail cars.
Energy Industry
The energy industry leverages aluminum forging to produce components for power generation, oil and gas extraction, and renewable energy systems. These components must endure high temperatures, pressure, and corrosive environments.
Turbine Components: Forged aluminum parts, such as turbine blades and housings, are used in wind turbines and hydroelectric plants due to their lightweight and corrosion resistance.
Heat Exchangers: Aluminum forged heat exchangers are used in power plants and refineries to efficiently transfer heat while resisting corrosion.
Drilling Equipment: Components such as drill collars and connectors are forged from aluminum to withstand the harsh conditions of oil and gas extraction.
Construction
In the construction industry, aluminum forging is used to produce lightweight and durable components for buildings, bridges, and infrastructure projects. The corrosion resistance and strength of aluminum make it ideal for structural applications.
Structural Components: Forged aluminum beams and columns provide the strength and durability needed for modern construction while reducing the overall weight of structures.
Fasteners and Connectors: Aluminum forged fasteners and connectors are used in construction projects to ensure reliable and long-lasting connections.
Scaffolding: Forged aluminum scaffolding components are lightweight and easy to assemble, improving safety and efficiency on construction sites.
Hardware Tools
The hardware tools industry benefits from aluminum forging to produce lightweight and durable tools that enhance performance and ease of use. Aluminum forged tools are ideal for both professional and DIY applications.
Wrenches and Sockets: Forged aluminum wrenches and sockets are lightweight and strong, making them easy to handle and durable for heavy-duty use.
Pliers and Cutters: Aluminum forged pliers and cutters provide the strength and precision needed for various cutting and gripping tasks.
Tool Handles: Forged aluminum handles for hammers, screwdrivers, and other tools offer a comfortable grip and reduce user fatigue.
Aluminum forging is a highly versatile and efficient manufacturing process that offers numerous advantages, including lightweight, high strength-to-weight ratio, and excellent corrosion resistance. Its unique properties make it an ideal choice for a wide range of applications across various industries. In the rail transit industry, aluminum forging is used to produce lightweight and durable components for trains and rail infrastructure. The energy industry benefits from its lightweight and corrosion-resistant components for power generation and oil and gas extraction. In construction, aluminum forged parts provide strength and durability for structural applications, while the hardware tools industry leverages its lightweight and durable properties to enhance tool performance.
As a manufacturer, leveraging the capabilities of aluminum forging can help you deliver high-quality, lightweight, and durable components that meet the specific needs of your customers. Whether you are producing parts for rail transit, energy, construction, or hardware tools, aluminum forging offers a reliable solution for achieving superior results. Its ability to reduce weight and enhance performance makes it a cornerstone of modern manufacturing in industries where efficiency and durability are paramount.