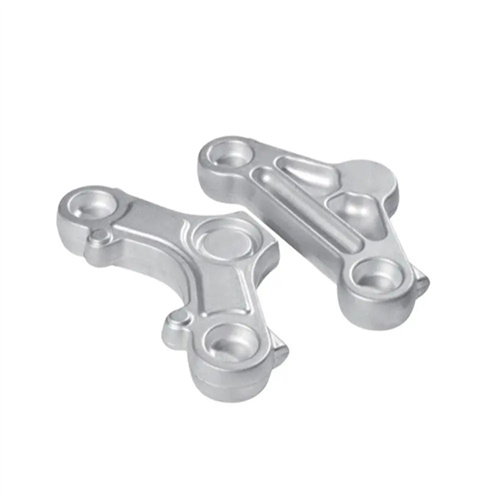
Custom Forging Parts
Custom forging parts are specialized components manufactured through the forging process, tailored to meet the specific requirements of a particular application or industry. Forging is a manufacturing method that involves shaping metal using compressive forces, typically at high temperatures, to produce parts with superior mechanical properties, such as strength, durability, and resistance to fatigue. Custom forging allows for the creation of unique, high-performance components that are designed to fit precise specifications, including complex geometries, tight tolerances, and specific material properties.
The forging process can be applied to a variety of metals, including alloy steel, aluminum, stainless steel, and titanium, depending on the application’s needs. Custom forging parts are widely used in industries that demand high reliability, precision, and performance under extreme conditions.
Advantages of Custom Forging Parts
Superior Strength and Durability: Forged parts have a refined grain structure, making them stronger and more durable than cast or machined parts.
Customizability: Custom forging allows for the production of parts with unique shapes, sizes, and material properties to meet specific application requirements.
High Precision: Forging can achieve tight tolerances and complex geometries, reducing the need for secondary machining.
Cost-Effectiveness: Forging minimizes material waste and often eliminates the need for additional processing, lowering overall production costs.
Resistance to Extreme Conditions: Forged parts can withstand high stress, temperature, and corrosive environments, making them ideal for demanding applications.
Applications of Custom Forging Parts
Heavy Machinery
In the heavy machinery industry, custom forging parts are essential for producing high-strength components that can withstand extreme operational conditions. These parts are critical for ensuring the reliability and longevity of heavy equipment such as excavators, bulldozers, and cranes.
Gears and Shafts: Custom forged gears and shafts are used in heavy machinery due to their high strength and wear resistance, ensuring smooth operation under heavy loads.
Hydraulic Components: Forged hydraulic cylinders, pistons, and valves provide the durability and precision required for heavy-duty applications.
Crankshafts: Custom forged crankshafts are used in engines and machinery to convert linear motion into rotational motion, offering exceptional strength and fatigue resistance.
Rail Transit
The rail transit industry relies on custom forging parts to produce critical components for trains, locomotives, and rail infrastructure. These components must withstand high stress, vibration, and wear over long periods of operation.
Wheels and Axles: Custom forged wheels and axles are essential for rail vehicles, providing the strength and durability needed to support heavy loads and ensure safe operation.
Couplers and Yokes: Forged couplers and yokes are used to connect rail cars, offering high tensile strength and resistance to impact forces.
Brake Systems: Components such as brake discs and calipers are custom forged to ensure reliable performance under high-stress conditions.
Energy Industry
In the energy industry, custom forging parts are used to produce components for power generation, oil and gas extraction, and renewable energy systems. These components must endure high temperatures, pressure, and corrosive environments.
Turbine Shafts and Blades: Custom forged turbine shafts and blades are used in power plants and wind turbines, offering high strength and resistance to thermal fatigue.
Valves and Fittings: Forged valves and fittings are used in oil and gas pipelines, providing durability and leak-proof performance under high pressure.
Drilling Equipment: Components such as drill bits and connectors are custom forged to withstand the harsh conditions of oil and gas extraction.
Power Equipment
The power equipment industry uses custom forging parts to manufacture components for generators, transformers, and other electrical systems. These components must deliver reliable performance under high electrical and mechanical stress.
Generator Rotors: Custom forged rotors are used in generators to convert mechanical energy into electrical energy, offering high strength and resistance to deformation.
Transformer Cores: Forged cores are used in transformers to enhance magnetic properties and ensure efficient energy transfer.
Circuit Breakers: Custom forged components in circuit breakers provide the strength and durability needed to handle high electrical currents and ensure safety.
Custom forging parts are critical components in various industries, offering superior strength, durability, and precision. Their ability to meet specific application requirements makes them indispensable in industries such as heavy machinery, rail transit, energy, and power equipment. In heavy machinery, custom forging parts are used to produce gears, shafts, and hydraulic components. In rail transit, they ensure the reliability of wheels, axles, and brake systems. The energy industry relies on custom forged parts for turbine components and drilling equipment, while the power equipment industry uses them for generator rotors and transformer cores.
As a manufacturer, leveraging the capabilities of custom forging can help you deliver high-quality, durable, and cost-effective components that meet the specific needs of your customers. Whether you are producing parts for heavy machinery, rail systems, energy infrastructure, or power equipment, custom forging offers a reliable solution for achieving superior results. Its ability to withstand extreme conditions and deliver long-lasting performance makes it a cornerstone of modern industrial manufacturing.